|
|
Systematic Quality Assurance -
The checkweighers series CPS are suitable for
installation after any packaging system in order to
provide an effective weight control of both, single
packages, and total production. Once the tolerance
limits of the checkweigher have been set the overweight
packages can be either rejected or accepted while the
underweight ones will be always rejected.
Optional integrated metal detector will ensure that
metal contaminated packs, are rejected from the
production process.
Several models of checkweighers are available,
in order to suit different weights and sizes of tested packages.
Weight range:- |
1,5 kg |
5 kg |
25 kg |
Accuracy:- |
+/- 0.5 gr |
+/- 5 gr |
+/- 10 gr |
Max. throughput pc/min:- |
180 |
40 |
30 |
Scale graduation:- |
0,1 gr |
5 gr |
10 gr |
Calibration:- |
continuous - automatic |
Weighing cell:- |
strain gauges |
Products memory:- |
100 |
Weighing belt size:- |
435 x 200 |
800 x 460 mm |
Product max. size:- |
320 x 200 |
600 x 400 mm |
- Sturdy structure made of painted or stainless
steel, designed to absorb vibration.
- Possible adjustment of the checkweigher
conveying levels from 750 to 1100 mm without
mechanical modifications.
- Package transportation made up of three
independent conveyors, with speed adjustable
through the operator interface panel.
- Easy cleaning and quick conveyor belt
replacement with no need to disassemble any
other components of the checkweigher.
- Automatic rejectors for products with incorrect
weight.
- Operator interface touch-screen type colour
panel for memorization, control and
self-diagnostic of all the machine operation
parameters, and fault debugging functions.
- Internal drives allows for storage of various
production reports, and software updates.
- Supplied with Ethernet, RS232, parallel port
and USB port.
- Weight processing by means of analogue to
digital converter and DSP with implementation
of advanced digital filtering technology.
- Electronic DSP (Digital Signal Processor) based
on microprocessor Motorola 16 bit 80 MHz
microprocessor.
- Continuous self-calibration cycle whenever
weighing station is empty.
- Possibility to set up and recall 100 different
production programs.
- Production parameters can be modifier during production runs.
- Two different levels of password, one for setting
up the working parameters (operator level) and
one for the special parameters (manager level).
- 24-column local printer for production reports.
- Production status, and weight classification
indicated by beacon lights.
- Connectivity to various SCADA software,
allowing automatic setting of production
parameters, real time statistics, and diagnostics
from remote location.
- Statistics programs to gather and send to a
central PC production data from several
checkweighers.
- Feed-back control for various filling, dosing
systems is providing complete net weight control.
- Integrated metal detector.
Complete turn-keys food processing and packaging solutions are available on request.
Please contact us on info@jzw.com.au to discuss your application. |
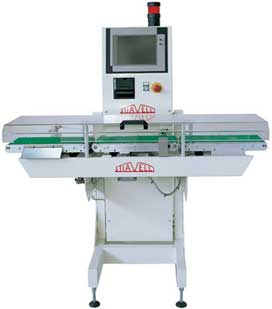
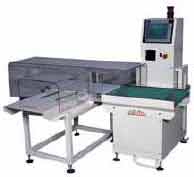
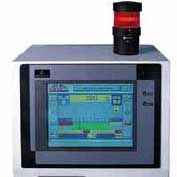
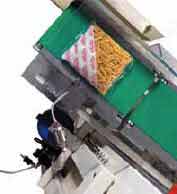
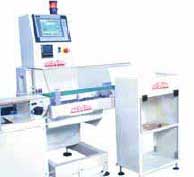
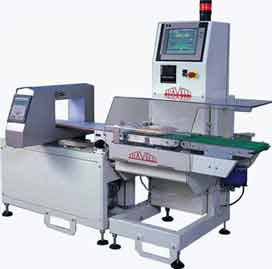
|