|
|
SVMA Stiavelli Intermittent Motion Vertical Form Fill Seal
machines for bagging various products -
SVMA Versatile VFFS Vertical Form Fill Seal
machines.
Stiavelli SVMA is a intermittent motion vertical
form fill seal bagging machine available in
pneumatic and electronic versions.
Among the various solutions of vertical
packaging machines proposed by STIAVELLI to
its large clientele, the new intermittent motion
packaging machines of SVMA series are
characterized by their simple and strong
manufacture and huge flexibility in several
applications such as short cut pasta as well as
granular products like fresh pasta, dry fruit, rice,
legumes, biscuits, candies and powders.
This new machine series is produced both by
pneumatic and servo motors powered versions and
there is also the possibility to make the machine
structure of stainless steel, with fixed inclination,
double pipe (twin). The filling of the product is controlled by one of
several different dosing systems; Multihead
Combination Weighers, Volumetric Filler, Auger Filler,
Pendular Weighers, or special systems.
Vertical packaging machines with body specifically
designed according to the sanitary requirement and
principle of the Food Industry (FDA-USDA-HACCP)
with body entirely in Stainless steel Aisi 304, for the
alternate production of pillow bags from reels of
thermo-salable film or sealable by impulse
(High density polyethylene), suitable for fin and/or
lap seal, regular or reverse for heat sealable film or
lap seal for plain polyethylene film.
The machine is intended as equipped with the
following features: - FILM UNWINDING UNIT, composed of a structure entirely in stainless steel Aisi 304 , shaft with expansion blades.
It is provided with a motorized adjustment for a prompt and easy adjustment of the film horizontal centring with respect to the forming set and a quick splicing unit, which eases and minimizes the required time for joining the film and replacing the reel.
The reel holder and breaking unit are provided with roll end detector.
It is provided with devices for the film compensation, necessary when the encoder or the photocell are used to obtain a rapid centering either of the stamping on the film or of the code print on the bags.
Encoder is set as close as possible to the collar of the forming tube, in order to always grant the best accuracy in the cut length.
- PULLING BELTS, driven and controlled by A/C motor with its inverter.
The positioning with relative pressure of the belts against the forming tube occurs by means of D/C motors through the touch screen, with adjustable pressure and sensor for avoiding excess of pressure against the forming tube.
The driving belts are directly driven, without articulate joints and without hidden, overlapped or hollowed components, designed and featured to be easily cleaned and sanitized, with specific meaning to avoid any possibility of stagnation and proliferation of germs and bacteria.
The replacement of the driving belts has been designed to be direct, without dismantling any component.
- VERTICAL SEALING JAW ASSEMBLY, composed of a fix arm sliding through linear bearings, with easy lock by means of a knob. The centering of the vertical arm is granted by a graded plate, easily readable. The motion is granted by a pneumatic cylinder SMC (METAL ON METAL). The distance of the sealing bar from the forming tube is adjustable by means of a knob.
- HORIZONTAL SEALINGJAW ASSEMBLY set on plates made of stainless steel AISI 304 and sliding through eight linear bearings ( four for each sealing jaw) Featured for the easiest and most efficient cleaning and sanitation operations.
The sealing bars, made in hard steel C 54, are provided with a particular device for removing, replacing or cleaning and re-setting the knife after operation without tools.
The motion occurs by means of a SERVO MOTOR.
SEALING JAWS TEMPERATURE CONTROL: exclusive and highly efficient system for the sealing jaws temperature control by means of which resistors power is being reduced or increased in proportion to the approach of the temperature at the set value. The wave of the temperature is always in a very narrow range of ± 3 º C.
- PHOTOCELL for film centering, complete with supports and electric connection to the packaging machine.
- AUTOMATIC FILM TRACKING SYSTEM by means of optical fibres which controls and eventually adjust automatically the position of the film respect to the center of the forming tube by moving the entire film unwinding unit through a DC motor.
- ELECTRIC PANEL made in stainless steel Aisi 316, protection grade IP 67, containing all the electro-mechanical components, the Programmable Logic Controller (PLC) OMRON and all the electric and electronic equipment, opening on hinges made of stainless steel, especially designed to avoid the stagnation and the proliferation of germs and bacteria.
- CONTROL PANEL touch screen type, set on the side of the electrical panel cabinet.
The screen allows the operator to set and visualize all the various machine operating parameters: timings, speed, sealing jaws temperature, bag counters and many more functions.
It also has the function of an alarm message display unit, providing information on the operating conditions of the machine and on any malfunctions; for example, it can display the piece counter, indicate absence of pressure, presence of film broken, etc.
The electric system is set, in its standard configuration, to accept various accessories: photocell, printer, etc. and the interface with the multihued weigher.
- THE MACHINE IS PROVIDED WITH THE SAFETY DEVICES AND WITH ALL THE PROVISIONS REQUIRED BY THE LAWS IN FORCE FOR ACCIDENT PREVENTION IN COMPLIANCE WITH THE NORMS UNI EN 415-3 and UNI EN 1672-2
- Easy comprehension of Electronic Management
of all machine parameters.
- Extremely versatile machine with possible
coupling with any kind of weigher (linear or
multihead combination weighers) or volumetric
doser (bucket or auger model).
- Reduced machine dimension and operating
functions particularly ergonomic with easy manual
regulations.
- Frame engineered to easily allow maintenance
and cleaning.
- Epoxy painted carbon steel structure with
polyurethane finishing, or stainless steel
Aisi 304/316.
- All product contact parts are food grade
stainless steel.
- Operator interface touch-screen type color panel.
- Control by PLC with all movements driven
by a mix of mechanical- pneumatic systems
or totally mechanical.
- Reel holder shaft with expansible device by
mechanical adjust in order to easy change reel.
- Speed and cycle control in phase.
- Film drive by lateral belts, film centering by
photocell and metering encoder for continuous
in-print film.
- Longitudinal and transversal sealing by hot bar type.
- Transversal cut by blade.
- Manual splicing of film reels (optional automatic
version).
- Stainless steel structure.
- Sealing group for polyethylene (PE) packaging
material.
- Film unwinding roll group with automatic
adjusting of the film transversal sliding and
reel end control system.
- Product unloading timing shutter driven by
pneumatic system or brushless motor.
- Gas flushing device.
- Device for making euro slot or euro hole bags.
- Device for making bellows bags.
- Device for making flat bottom bags with fin.
- Device for coupling with clipping machine.
- Devices for making 4-side seal bags.
- Coders / printers Mod. Data
Complete turn-keys food processing and packaging
solutions are available on request.
Please contact us on info@jzw.com.au
to discuss your application.
|
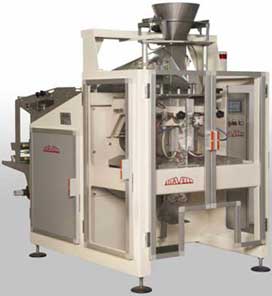
|